ISO 13655:2009 Demystified
Why do we have M0, M1, M2 and M3?
The purpose of this document is to explain in both theory and practice the measurement modes M0, M1, M2 and M3 defined in ISO 13655:2009.
ISO 13655 defines the needs for spectral measurement equipment for the graphic arts industry.
It references the international standards ISO 5-2 and ISO 5-4 for density measurements and CIE15 for general terminology of colorimetry.
There are prerequisites that have to be fulfilled by instruments regardless of measurement mode.
One important prerequisite is the fulfilment of the measurement geometry. ISO 13655:2009, as stated, references ISO 5-4 which unambiguously defines that only one of the following four geometries may be used:
- forty-five degree annular: normal 45°a:0°
- forty-five degree circumferential: normal 45°c:0°
- normal: forty-five degrees annular 0°:45°a
- normal: forty-five degrees circumferential 0°:45°c
No other geometries are recommended.
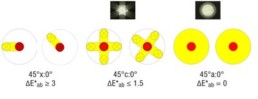
ISO 13655:2009 Annex C reads:
“If, however, sensing and/or irradiation is limited to a single azimuthal angle, directional and texture effects are emphasized. These geometries are deprecated in ISO 5-4 and hence in this International Standard. They are known as “forty-five degrees directional: normal” and “normal: forty-five degrees directional”.
In other words when instruments with a directional geometry are used, results will be highly dependent on the measurement angle. When turning the spectrophotometer by some degree the same sample will give different readings. This effect gets stronger with increasing texture and on uncoated papers a colour difference of more than dE*ab = 3 can be experienced.
Q: How can users find out if a certain instrument conforms to the geometry requirements of ISO 13655?
A: The specification sheet of an instrument usually states the geometry. If this is not “45°a:0°” or “45°c:0°” (or the other way round) but only 45:0 most likely the requirements are not met. Also stating a conformance to DIN 5033 does not mean that the instrument conforms to ISO 13655. DIN 5033 simply describes all existing measurement geometries.
Having met the prerequisites of measurement geometry, an instrument conforming to ISO 13655:2009 can comply with 4 different measurement modes. These modes were developed due to different needs and applications. They are called M0, M1, M2 and M3.
M0: “The Legacy Mode”
From a purely technical point of view, M0 is an obsolete measurement mode. Historically instruments used in the graphic arts industry did not use a light source with a defined and/or stable UV content. M0 as a standard expresses that the majority of instruments use a gas-filled tungsten lamp to illuminate the samples rather than D50 and therefore users accept a known weakness.
The problem with unstable and undefined UV content is that when measuring fluorescent samples such as papers with optical brighteners, the measurement response does not correlate with the viewing environment where the printed product is used. Although many users have chosen to ignore it, the UV content of a gas filled tungsten lamp also changes over time which means that measurements are unreliable.
For legacy reasons and to compare measurements with existing instruments, the Konica Minolta FD-series spectrodensitometers offer the choice of measurement mode M0. Here the spectral power distribution of CIE illuminant A (which is recommended in ISO 13655:2009 for M0) is used to illuminate the sample. Due to the stable UV-content in the Konica Minolta instruments users can at least rely on stable measurements if they need to use M0 for legacy reasons.
Take-home message:
M0 = undefined light source. If you measure samples with optical brighteners you should be aware of the disadvantages.
The following paragraphs will explain M2 and M3 before details regarding M1 which requires more explanation.
M1: “The All Time Desired Mode”
The graphic arts industry uses standardized viewing conditions in order to minimize issues when communicating colour. The relevant standard is ISO 3664, which specifies CIE illuminant D50. Since 2009 the UV-content of D50 has to be met within closer tolerances than before. In order to make sure that optical brighteners “glow” to a similar extent when illuminated during a colour measurement as they do in a D50 viewing environment, ISO 13655 introduces the measurement mode M1. Compliance to M1 can be achieved in two ways.
Method 1: Illuminant Match
M1 can be achieved by using a light source that fulfils the requirements of ISO 3664:2009. This simply means, that if you build a normlight into the spectrometer, it complies to M1 (but remember the prerequisite of geometry). This sounds simple but can not be achieved in practice.
The obvious choice of using the same light source as used in most viewing cabinets can’t be realized as these are mostly fluorescent lamps which cannot be built into a spectrophotometer. In addition they do not perfectly match CIE illuminant D50 (approximation within defined tolerances).
Another possibility for achieving D50 is to use a combination of different LEDs, which produce a D50 spectrum. In practice a problem occurs when trying to mimic the UV content of D50 as current LEDs are not capable of perfectly reproducing the UV content of D50.
The last presented technical solution for achieving D50 as physical illumination is to use filtered light sources to mimic the spectral power distribution of D50. The advantage is that with this technique a close match to D50 can be achieved. This should also provide correct measurements for samples that show fluorescence active in the visible wavelength area (few inks and toners do show this behaviour to some extent). The disadvantage is that the light source might not be stable in terms of its UV content and therefore reliability over time has to be questioned.
Furthermore we have to ask ourselves if perfect D50 is really the best solution to be used in a measurement device. Normally we do not have perfect D50 as a viewing condition but only a simulation within tolerance. So the theoretical benefits can hardly be transferred to practical usage. How this problem is overcome will be explained later in this document.
Method 2: UV Calculation
The second possibility to achieve conformance to measurement mode M1 is related to the nature of optical brighteners. Optical brighteners absorb UV energy and emit blue visible light. To measure the effect of an optical brightener it is perfectly sufficient to assure a correlation between brightener excitation during the measurement and in the desired viewing environment. This is described by means of the ratio between UV-content and visible content in ISO 13655:2009.
In other words: Make sure that during the measurement the brightener glows as bluish as in your desired viewing environment.
This can be achieved in different ways. In the available literature some methods are described. Two will be discussed in the following.
As discussed, an optical brightener absorbs UV energy and emits this energy as blue light. Should we like to measure the amount of emission for a certain reference illuminant, we need to assure that the light source in the measurement device has enough energy in the wavelength area where the optical brightener is active.
If you were able to conduct two measurements, one using only UV energy, to give pure fluorescence, and the other without UV energy to provide pure reflectance, it was possible to calculate the resulting total radiance factor (often called reflectance factor although it is the combination of reflection and fluorescence).
The problem is that the method relies on the existence of a UV-only light source. The UV-LEDs that are available today have a varying spectral power distribution and also emit visible light. Thus not only fluorescence but also reflectance (caused by the visible light emitted by the UV-LED) are measured and introduce errors into the underlying model. Real-life instruments using this method would suffer from a varying measurement error.
M2: “UV-Cut”
The measurement mode M2 was standardized in order to reflect viewing conditions that are free of any UV content such as in a museum. Thus it is often referred to as “UV-Cut”. In the past spectrophotometers equipped with a UV-Cut filter were used in order to ignore the effect of optical brighteners. It was thought this would make the calculation of ICC profiles easier as UV-introduced metamerism did not effect measurements. The misconception that optical brighteners disturb colour measurements is still present among users (and to some degree vendors), indeed many digital printing machines are still delivered with UV-filtered instruments.
Optical brighteners do glow bluish depending on the UV-content in the viewing environment (and the light source of the measurement device). If a UV-filtered instrument leads to more pleasing results than an instrument with a tungsten lamp, the UV-content of the viewing environment is simply closer to UV-Cut than to the UV-content of a gas-filled tungsten lamp.
But most likely it is not UV-free (unless you work next to the Mona Lisa). Thus M2 is not the appropriate solution for most applications and it is only standardized to reflect UV-free viewing conditions.
The Konica Minolta FD-series spectrodensitometers offer the choice of measurement mode M2. Here the definition of a UV-Cut filter from ISO 13655:2009 is met.
Typical production papers in environments with different levels of UV
Figure 2: Typical production papers in environments with different levels of UV.
Take-home message:
M2 = UV-Cut. It’s only useful for UV-free environments.
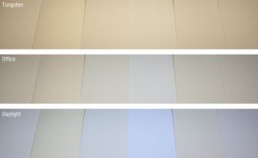
M3: “The offset printers’ mode”
The challenge faced by Offset printers is that they need to control wet sheets during production but the customer pays for the final product which is dry. The biggest difference between wet and dry sheet is the gloss. Measurement mode M3 offers means to predict the density of a dried sheet from a measurement of a wet sheet. This is achieved by using two polarization filters, which minimize the difference in gloss.
The Konica Minolta FD-series spectrodensitometers offer the choice of measurement mode M3 by attaching a polarization filter-glass.
Take-home message:
M3 = Pol-Filter. Needed for offset printers. Some ink manufacturers also use M3 for CCM.
Konica Minolta Virtual Fluorescence Standard
The second method works in a similar way but does not rely on the existence of a pure UV light source. When using the Konica Minolta Virtual Fluorescence Standard the UV element of a sample is activated by two light sources with vastly different UV energy consecutively (within milliseconds and not visible to the user). Should the sample show fluorescence, the resulting radiance factors (the “measurement result”) will differ. By this method it is easy to distinguish fluorescence from reflectance. By incorporating the UV-content of the final viewing environment it is possible to calculate the correct total radiance factor.
The clear advantage of this method is that it does not rely on impractical or non existent (UV-only) light sources. The Konica Minolta FD series measure and stabilize the light sources used within them and having a stable base for the calculation ensures stable and repeatable measurements even if the physical light sources between different instruments differ.
Another advantage of the Konica Minolta FD series relates to the viewing environments that are used. Even if standardized light sources are used, commercially available viewing cabinets are in tolerance of ISO 3664:2009 but do not emit perfect D50. Using the Konica Minolta VFS it is easy to quantify spectral characteristics and use the viewing cabinet as a measurement light source. By using the FD-7 users can objectively determine colour values that perfectly correlate with the visual impression. The User-Illuminant function eliminates the problem of variations in approximated D50 generated by viewing cabinets. This is of course not limited to D50 simulators but is also beneficial to get colour matches for light conditions ‘on site’ or at trade-fairs.
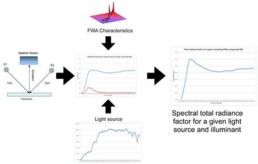
Both methods follow the assumption that the excitation wavelength and emission wavelength of the optical brighteners used in papers do not vary. This assumption is valid but only Konica Minolta has built commercially available measurement equipment to determine the exact characteristics of this class of brighteners (CM 3800d).
As the UV calibration of the FDs is not fixed to D50 (for example D65 can also be used) the values measured with an FD correlate very well with instruments used in the paper industry, although the instrument geometry is different.
Conclusion
The Konica Minolta Virtual Fluorescence Standard has serious advantages over other methods described in this paper and implemented in practice. In short these are:
- Stable measurements
- Opportunity to use real light sources as reference illuminant
- Traceability to a bi-spectral measurement device (CM3800d)
- Opportunity to get values correlating with instruments used in the paper industry