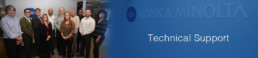
Service FAQs
We cannot stop production while our unit is in for service. How long is the repair time turnaround?
We offer an expedite service (additional charge) which has a 48hr turn around time after we receive the unit.
My warranty is about to expire. Does Konica Minolta offer an extended warranty?
Konica Minolta offers a technology insurance program (TIP) which is available at different levels, depending on your needs. Please visit Extended Warranty & Calibration Plans page for more information.
What does your service warranty contract include?
The contract includes all parts and labor with the exception of the sphere. The warranty will also be voided if there is evidence of tampering or user mishandling. Please visit Extended Warranty & Calibration Plans for more information.
What should I include when sending my unit in for service?
Please send in all masks, cables, AC adapters, the calibration plate and any other accessories that need to be tested or calibrated to the unit.
Our company is ISO:9001 certified. Do you offer documentation with a serviced unit?
All units are returned with either a Certificate of Calibration or a Certificate of Conformance, depending on the model.
Do I need to calibrate my unit everyday before I perform measurements?
Yes. You should calibrate to your standard before you perform your measurements. Most units will ask you to calibrate if you have not already. Please visit Daily Calibration page for more information.
How often do I need to send in my unit for calibration?
Konica Minolta suggests that you send in your unit for calibration yearly due to use of unit; degradation of white plate, etc. Please visit Calibration page for more information.
What is the difference between factory calibration and daily instrument calibration?
Both factory instrument calibration and daily instrument calibration are important to maintaining consistent and reliable readings from your color measurement instrument. Both calibrations must be current, and are necessary to ensure the instruments highest performance. You can’t have one without the other. Please visit Calibration page for more information.
What is daily instrument calibration?
Please visit Daily Calibration page for more information.
How often should daily calibration be performed by the operator of the instrument?
Please visit Daily Calibration page for more information.
What is factory calibration and why is it required to perform this annually?
Factory calibration, also referred to as annual calibration, is a much more comprehensive testing and re-calibration of an instrument. Factory calibration is the process of adjusting the accuracy of the instrument in comparison to a master instrument and standards which meet known national or international traceable standards. Daily calibration and factory calibration share the same goal, making sure your instrument is reading accurately and repeatable. The two go hand in hand and neither can replace the other.
Every new Konica Minolta Sensing Americas Instrument ships with its factory calibration assured. This baseline factory calibration is what ensures your daily calibrations can be completed correctly and accurately. Your daily calibrations are tied to the accuracy of the instruments factory calibration. To ensure instruments will function correctly over time it is necessary that all color measurement instruments receive factory calibration on an annual basis. Please visit Annual Calibration page for more information.
A brief overview of the differences between factory calibration and daily calibration is:
- Factory calibration can only be performed by a trained and certified Konica Minolta Sensing Americas service technician either in our state of the art calibration laboratory in Ramsey, NJ, or at the instruments location by one of our field service engineers.
- Ensures the instrument meets all of the measurement specifications as it did when it was newly produced. The specifications and methods to evaluate are traceable to in house master instruments and standards which are traceable to standards organizations such as NIST, NPL, etc…
- Assess the instruments overall ability to read color through the entire spectrum both for accuracy and repeatability.
- Evaluates and if needed corrects through repair the instruments physical state, such as optics, lamps, apertures, etc…
- Recalibrates and assigns new calibration values to the white calibration tile used for daily calibration.
Issues new traceable certificates for both the instruments factory calibration, and the standard white calibration tile. - Please visit Calibration page for more information.